Common Elevator Problems and Solutions
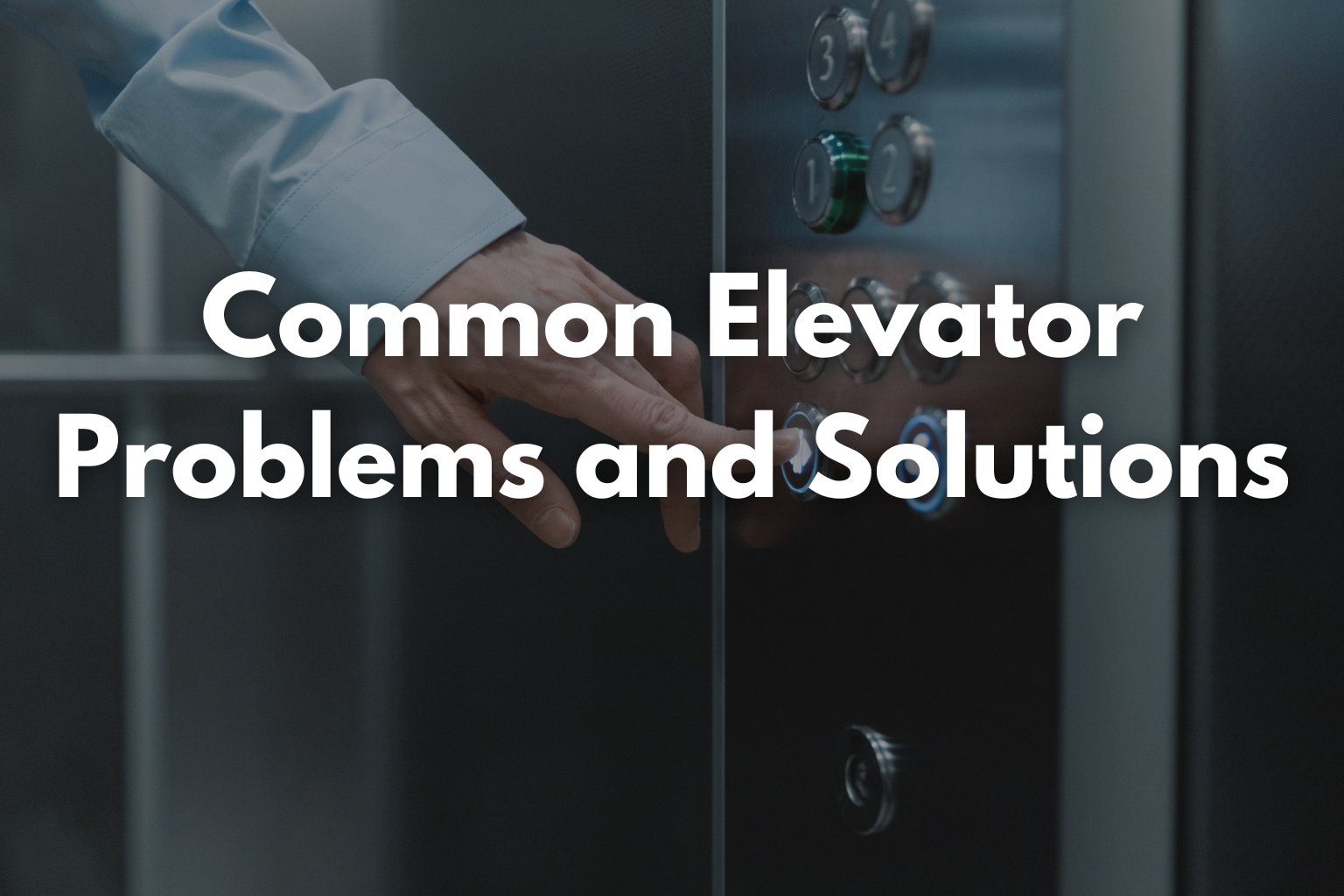
Table of Contents
Having to deal with continuous elevator breakdowns and malfunctions? Concerned about your building’s elevator safety and efficiency? If so, you are not the only one. Many common elevator problems can disrupt daily routines and cause inconvenience.
In this article, I will explore some common elevator problems and provide solutions to help you overcome these issues and ensure a smoother elevator experience for you and your building’s occupants.
Key Takeaways:
- Regular maintenance and inspections are key to preventing common elevator problems and ensuring the safety of elevator users.
- Elevator problems commonly occur due to power outages, mechanical breakdowns, and sensor malfunctions.
- To resolve elevator problems, troubleshooting techniques, power source checks, routine maintenance, and part replacement can be effective.
What Are Common Elevator Problems?
Common elevator problems often arise from issues within the elevator system, resulting in frequent breakdowns and interruptions.
These common faults include:
- door malfunctions
- electrical problems
- irregular movements
Elevator motors and control systems can also overheat, leading to operational issues. Mechanical wear and tear can also occur over time on components such as cables, pulleys, and motors. Furthermore, sensor faults may also occur, which can impact the smooth operation of the elevator.
What Are The Causes Of These Problems?
Elevators are an essential part of our daily lives, providing convenient and efficient transportation in buildings of all sizes. However, like any mechanical system, elevators can experience various problems that disrupt their operation.
By understanding the causes, we can better understand how to prevent and address these issues to ensure smooth and safe elevator operations.
1. Power Outages
- Elevators can stop functioning due to failures in the electrical system or power line disturbances.
- Unstable power supply and electrical distribution issues can frequently trigger outages.
- Sudden voltage spikes or drops in the building’s power grid can impact elevator operations.
2. Mechanical Failures
- Regular use leads to wear and tear on critical components like motors and ropes, affecting performance.
- Mechanical parts can fail due to aging, lack of maintenance, or poor-quality materials.
- External contaminants, such as dust or water intrusion, can deteriorate mechanical systems.
3. Sensor Malfunctions
- Inconsistent power quality can cause sensors to malfunction or provide inaccurate readings.
- Sensors are sensitive to electromagnetic interference, which can arise from nearby electrical equipment.
- Issues with sensor alignment or faulty wiring can lead to operational disruptions in the elevator system.
4. Overweight Capacity
- Elevators can malfunction when loaded beyond their specified weight capacity.
- Overloading not only strains the mechanical system but also risks passenger safety.
- Exceeding maximum occupancy limits frequently leads to operational problems and potential breakdowns.
How Can These Problems Be Identified?
Elevators, like any mechanical equipment, can experience issues and malfunctions. However, these problems can be identified through various indicators.
This section will teach you about common elevator problems, including unusual noises, slow movements, doors not opening or closing properly, and error messages. We can troubleshoot and solve these issues by understanding their signs and symptoms.
1. Unusual Noises
- Listen for Noises: Listen to unusual noises during elevator operation, such as motor vibrations or noisy bearings.
- Investigate the Source: Identify the origin of the strange noises, as they may indicate damaged bearings or other mechanical issues.
- Consult Maintenance: Contact elevator maintenance professionals to promptly diagnose and address unusual noises.
2. Slow Movement
- Inspect the condition of the motor, ropes, and safety devices for wear and tear regularly.
- Monitor voltage levels and vibrations to detect potential issues affecting the elevator’s movement.
- Address contamination concerns to prevent interference with the system’s operation.
Pro-tip: Regularly scheduled maintenance can minimize downtime and enhance safety.
3. Doors Not Opening or Closing Properly
- Inspect for misaligned door tracks causing obstruction.
- Check for faulty door sensors triggering improper functioning.
- Examine worn-out door rollers hindering smooth movement.
- Evaluate the door operator system for malfunctions affecting door performance.
Did you know that elevator doors have sensors to prevent closing when an object is detected, ensuring passenger safety?
4. Error Messages on Display Panel
- Check for error codes or messages displayed on the elevator panel.
- Refer to the elevator manual to understand the meaning of the error messages.
- Contact a certified technician to diagnose and address the specific issue indicated by the error messages.
- Regularly inspect the control systems and parts to prevent faulty components, such as uneven floor surfaces, from triggering error messages.
Did you know? Faulty suspension ropes and irregular leveling are common causes of error messages on elevator display panels.
What Are The Solutions To These Problems?
The elevator is an essential part of our daily lives as it provides convenient and efficient transportation in buildings of all sizes. But unfortunately, like any mechanical system, elevators can experience problems that disrupt their performance.
This section discusses the solutions to elevator problems, including unresponsive lifts and power outages. Additionally, we will discuss the importance of routine elevator maintenance and the possibility of replacing faulty parts. By understanding these solutions, we can ensure that elevators operate safely and reliably.
1. Resetting the Elevator
- Locate the elevator control panel.
- Press and simultaneously hold the ‘Stop‘ and ‘Door Open‘ buttons.
- Wait for the unresponsive lift to reset and then return to normal operation.
Consider these DIY tips for troubleshooting, like checking power connections and sensor functionality. Preventive measures include regular maintenance and educating users about addressing lift issues promptly and safely.
2. Checking Power Source
- Check power lines for any signs of damage or disturbance.
- Inspect the electrical distribution system to ensure proper power is supplied to the elevator.
- Conduct a power quality survey to assess the stability of the alternating current.
- Verify the power factor to ensure efficient power usage.
Educate staff on basic power failure troubleshooting to prevent power-related issues and consider upgrading to modern elevator systems for better power management.
3. Performing Routine Maintenance
- Conduct proactive maintenance to identify and address potential issues before they escalate.
- Inspect and replace worn sheaves and inductive absorbers to prevent mechanical failures.
- Implement artificial intelligence for predictive maintenance, detecting problems before they occur.
- Focus on commercial buildings with high elevator usage, intensifying maintenance efforts.
4. Replacing Faulty Parts
Thorough inspection: Perform a complete evaluation to identify worn-out components and damaged parts.
Identify worn-out components: The parts that have deteriorated over time, such as cables, pulleys, or bearings.
Replace damaged parts: Install new components to address wear and tear, reducing friction and ensuring smooth operation.
Reduce friction: Implement lubrication or component replacement to minimize friction and improve performance.
How Can These Problems Be Prevented?
Elevators are essential to modern living, providing convenient and efficient building transportation. However, like any other machinery, elevators are prone to technical problems that can cause inconvenience and even safety hazards. Here’s a streamlined approach to preventative measures:
Regular Maintenance and Inspections
Tailored Inspection Protocols: Maintain elevators according to their age, usage, and type. The elevator service company will help you create customized inspection protocols to suit your elevator in optimal operating conditions.
Digital Maintenance Logs: Keep a digital record of all maintenance activities for transparency and efficiency.
Advanced Techniques and Technology
Laser Alignment Checks: Use advanced laser tools to calibrate elevator components precisely.
Automated Temperature Monitoring: Install systems to monitor and alert for temperature changes in critical parts.
Proactive Component Care
Eco-Friendly Lubrication: Choose environmentally friendly lubricants for better performance and reduced environmental impact.
Predictive Maintenance: Implement smart sensors and IoT technology to anticipate and address issues before they escalate.
Training and Safety Culture
Staff Training Programs: Regularly update maintenance staff with the latest elevator technologies and practices.
Safety Audits: Conduct audits to ensure adherence to safety regulations and industry standards.
Conclusion:
In conclusion. elevator problems commonly arise from power fluctuations, mechanical wear and tear, faulty parts, and overloads. The most common issues are doors, electrical systems, movements, capacities, and sensors. For smooth, safe operations, regular inspections and proactive maintenance are essential.
These include resetting, checking power sources, and replacing damaged parts. The owners of buildings can improve efficiency, convenience, and safety by understanding common problems and how to solve them.
Frequently Asked Questions:
How often should elevators undergo professional inspection and maintenance?
Elevators should be inspected and maintained at least once a year, but more frequently in high-traffic buildings.
Can software updates improve elevator performance and safety?
Yes, software updates can enhance performance, safety, and energy efficiency in modern elevator systems.
What is the impact of weather conditions on elevator operation?
Extreme weather can affect power supply, increase moisture and dust intrusion, and lead to mechanical wear.